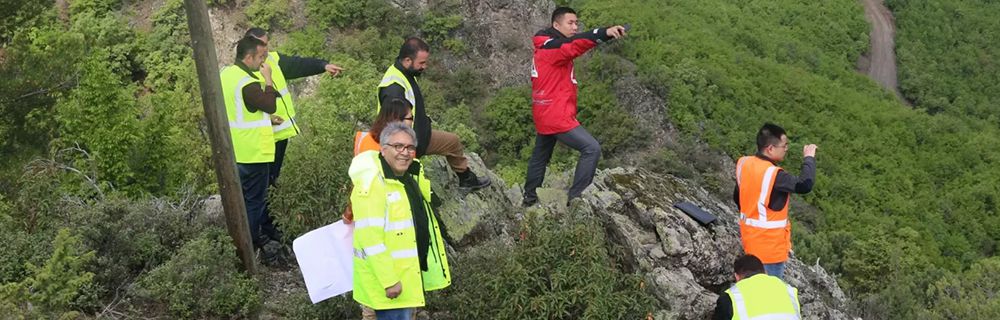
Our customer service team is always delighted to provide a variety of service options that are specifically oriented to your production needs. Our passionate engineers and technicians are responsible for providing quality maintenance and repair service at customer sites, or conducting regular safety inspections on compliance with the relevant legislation. Our comprehensive warranty will provide you with additional protection if any failure occurs with our equipment.
We provide replacement parts to our global customers through our worldwide service network. We'll assign a customer service representative to assist you with technical questions and support for your online repair requests. Replacement parts are available in conveyor belts, drive gearboxes, pulleys, gear rims, slewing bearings, pivot bearings, winches and other original spare parts and wear parts.
Our hotline help is given 24 hours a day, seven days a week by multi-talented engineers who have been engaged in on-site experience for over 4 years. In general, our engineers will work remotely to solve your problems. If the issue requires more specialist attention, our engineer will be dispatched as soon as possible for on-site troubleshooting service.
Our training service is precisely tailored to your individual requirements and delivered at your location or at our plant, aiming at ensuring that your employees are highly qualified to operate the equipment and maintain high operational performance.
Our specialty lies in offering unique solutions to meet your specific needs. Our engineers will identify the best equipment to accommodate your environmental conditions and requirements. In addition to technical data regarding bulk material handling equipment, we can also provide you with following information:
- Delivery time
- Equipment operation and maintenance
- Quotation and shipping cost
- Environmental and safety measures
- Integrating with existing equipment
Please use links or fill out the form with your request. Our customer service department will look closely at your needs and work out a tailored solution.
We also provide services below:
- Mine planning
- Equipment design and layout
- Pricing
- Profit engineering
Deviation: The accuracy is guaranteed in the equipment installation stage, so that the probability of deviation during operation is relatively small. If it occurs, there are generally the following reasons:
- Whether the blanking deviates from the center of the belt.
- Whether the head and tail rollers have debris or the rubber surface is wet.
- Whether there are idlers or the idler frame is loose.
Generally, for long-distance belt conveyors, there will be no deviation in the middle of the belt conveyor, and the main focus is on the deviation of the head and tail.
Scattering: Scattering at the receiving point and the discharging point is common. If it occurs, it is necessary to check the sealing condition of the sealing strip, guide the material flow, avoid direct impact friction, and check whether the size of the material opening matches the throughput.
Damage to the idler: The life of the idler is generally more than 3 years. If the idler is damaged in a short period of time, check the installation height of the idler and the installation accuracy of the idler, and find the cause of the damage of the idler, so as to avoid the easy damage after replacement;
Abnormal noise: Abnormal noise is mainly the driving part and the drum. Generally, the abnormal noise is caused by the installation accuracy. If it is not eliminated in time, it is easy to cause equipment damage.